Recent advancements for more affordable and capable laser technologies are being combined with high-performance industrial robots, providing manufacturers with greater precision and flexibility (over traditional, yet reliable, robotic welding processes) for even higher productivity on the shop floor. Moreover, materials that were once seen in the industrial sector as non-weldable are now being fabricated with ease, often creating unique products while reducing waste.
Widely used to replace spot welding applications for aerospace, automobile and heavy equipment manufacturers, remote laser welding (RLW) – a non-contact laser welding technique – is starting to see an uptick in utilization for more complex applications in various industries, especially for high-volume manufacturing. While traditional robotic welding is still the preferred method for a wide range of tasks, applications that require the utmost accuracy and speed are a better fit for industrial robots equipped with remote laser welding heads. Whether you are just starting to learn about RLW or you are closer to making a robotic purchase, the following information may be helpful to your decision-making process.
Why Remote Laser Welding?
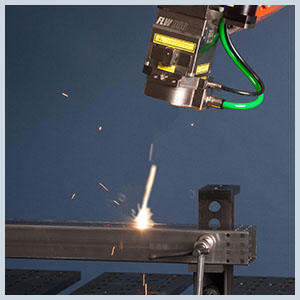
Remote Laser Welding is “remote” in that the laser head uses a longer stand-off of 100-150 mm for the beam to travel from the head to the point it is focused on the part. Fiber optics are used to pipe the laser beam to a laser head end-of-arm tool – greatly increasing flexibility of robot motion, minimizing interference and preventing costly damage due to a crash. A remote laser welding head then focuses and guides a laser beam rapidly with mirrors steered by galvanometer motors (low inertia, programmable servo motors).
This makes the robot accuracy a secondary factor, allowing manufacturers to implement traditional heavy payload robots, such as the
SP165 or a
GP180 for positioning the heads. Using a conventional-style robot like this, rather than a high-precision robot, like the
MC2000 II, is often less expensive and plays into a better target payback period.
Similarly, remote laser welding heads have special software, allowing programs to operate while the robot is moving. This is commonly known as welding “on-the-fly”. While a smaller number of applications use “on-the-fly” configurations, Yaskawa offers a feature that fires an output based on robot position, synchronizing the robot motion and laser head motion at the same point every time.
Is RLW Cost-Effective?
While laser welding still involves a large, capital expenditures for the laser, head and chiller, it continues to come down in price. To justify this type of initial capital investment, it is important to offset the cost by having enough volume. If high-volume production is a concern, speaking to a reputable robot supplier about the pros and cons of robotic laser welding vs. installing a welding robot with a spot gun and a timer for your particular application may be beneficial.
Similarly, robotic laser welding typically uses YAG lasers (a combination of yttrium, aluminum and garnet crystals) which have harmful light, requiring a light-tight enclosure. This adds additional expense and may be impractical for large
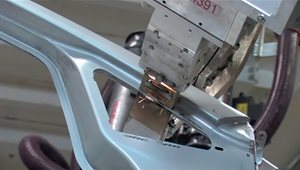
structures such as car bodies. To address the laser welding of larger parts, some laser welding heads utilize a “boot” surrounding the weld area, forming a light-tight seal. As seen with IPG’s Laser Seam Stepper (LSS), this localizes the light-tight enclosure requirement, but limits the length and range of the weld, making it an ideal replacement for spot or stitch style welds.
Is RLW the only way to laser weld?
The remote laser welding head provides the advantage of quickly moving the beam over a wide area and it may not require any robot motion while performing several welds in a given area. Robots can also present parts to a stationary RLW head to help share the load of keeping the “laser on” time high. RLW heads can also be used to manipulate the beam for non-welding applications, such as ablation for part cleaning.
A fixed head can be mounted on the end of the robot to allow the robot motion to move the beam. Even fixed heads may incorporate some beam manipulation that wobbles or oscillates the beam to make a wider weld, distributing heat, handling more joint variation and outgassing of vapors. Smaller payload, arc welding class robots may be combined with a wobble head in a smaller, lower cost workcell for smaller parts.
What Else Should be Considered?
Materials
As mentioned, laser welding is opening the door for the welding of next-generation materials. One such material that is often asked about is the new, ultra-high strength steel used in automotive and whether it is well-suited to laser welding vs. resistance spot welding. Because of the metallurgy of stronger strength steel, it is definitely a good candidate and can be responsive to rapid heat/cooling cycles of laser welding (better than slower resistance heating).
The use of aluminum for fabricating lighter weight trucks and for manufacturing automobile parts, such as electronic vehicle battery trays, is also quickly growing. As a result, the use of laser welding for the latter is gaining traction – as laser welding’s low heat input, high welding speed and great flexibility help manufacturers meet the strict requirements surrounding the weld process for car battery parts.
Methods
From resistance spot welding to friction stir welding, robotic laser welding is replacing certain processes, increasing quality and throughput. Specific types of laser weld processes that are being looked at quite heavily for a variety of robotic welding applications include hot wire and hybrid laser welding. Likewise, laser welding for cladding with wire and powder is gaining interest due to the speed and low heat input.
Joint Design
Lap joints with tight fit work best for laser welding. Minor gaps between surfaces can turn laser welding into laser cutting quickly and that is why fixtures for laser welding use high force clamping. Laser welding only requires single side access, unlike spot welding, but the bottom does need support to resist clamping forces.
Surface
The surface of the product being welded must be given some thought as well. Ideally, when using a laser for a product, a class A surface (a free form surface with an aesthetic shape and optimum surface quality) should be used. This is because the small heat effected zone cleans up quite well. For this reason, use for laser welding – in lieu of traditional resistance spot welding (RSW), gas metal arc welding (GMAW), or tungsten inert gas (TIG) welding – is expanding in industries like the home appliance industry, where stainless steel range hoods, ovens and refrigerators are made.
Skilled Resources
When programming a robot, it is critical that the operator understands the process which it is teaching the robot. A skilled robotics operator with arc or resistance welding experience may not fully understand the laser processes. For this reason and to get the most out of the process while maintaining part integrity, companies should consider hiring or training personnel to understand laser welding techniques. Volts, amps and wire feed speed are replaced with laser power and speed, not to mention the differences of shield gas and filler metal potentially used. Laser safety is also a critical factor that plant personnel will also be responsible for.
From joint geometry to part fit and more, there are a lot of facets to think through with robotic laser welding. If you are wondering if the robust quality and increase in throughput provided by robotic laser welding are a good fit for your company, it is wise to reach out to your preferred robot supplier to seek answers to your specific application questions.