In a competitive industrial landscape where unplanned downtime can cost you more than just a day’s amount of production, it is important to be proactive in finding the hidden inefficiencies, anticipating machine and robot failures before they develop. A form of organizational empowerment, having a predictive maintenance strategy that utilizes collected data and seeks to eliminate breakdowns before they happen is key.
What is the Life Cycle of an Industrial Robot?
Whether you’re dealing with an industrial robot or another piece of capital equipment, it is strongly advised to prevent (as much as possible) the deterioration of the asset. Where a robot is concerned it is important to understand that there isn’t a one-size-fits-all approach to maintenance, and there may be a bit of a learning curve when it comes to understanding how a particular robot functions. Regardless of individual robot quirks, the life cycle of a well-maintained robot should entail:
- Installation & Setup - The initial part of the cycle is focusing on efficient installation and proper setup of the robot and any peripheral equipment.
- Optimization - This next part of the cycle includes increasing throughput, increasing independence, reducing cycle time and reducing scrap. This phase typically is related to the process specific tasks (i.e., welding, material handling, etc.), so it is important to not only consider the robot, but the application as a whole.
- Maintenance Programs - During this stage, regular predictive maintenance, system audits and safety audits should take place – as having a comprehensive, value-added support program designed to ensure maximum robot performance and return on investment (ROI) over the life of an asset is a must to maintaining peak equipment performance.
- Continuous Improvement - This phase of the robot life cycle focuses on measuring, inspecting, analyzing and controlling the data that is collected during the maintenance programs.
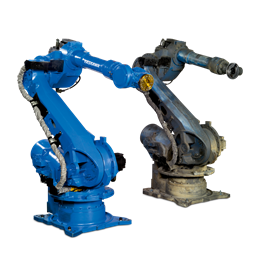
- Rebuild / Redeploy - While robots today are highly reliable and built to last many years, there comes a point that rebuilding and redeploying, or even replacing, becomes paramount. When this happens, a reputable robot supplier should be able to answer your questions and guide you through the process that is best for your operations.
For most Tier 1 suppliers, a well-maintained robot is one that is performing its regular duties with a 99% efficiency rate. This is ideal for most robots, and it is usually a good benchmark for manufacturers to follow.
What Should be Measured with Respect to an Industrial Robot?
Process Level Measures
It is vital to remember that the robot is only part of the big picture, and many times the robot is not necessarily at fault when a maintenance issue presents itself. Potentially, the part, fixturing or even programming (if being edited/modified when it shouldn’t be) could be at the crux of the matter. For this reason, looking outside of the robot and monitoring the complete functionality of the system is always a good idea.
Robot Level Measures
A robot is measured by overall performance (consistency, part quality and path accuracy) and internal functionality (grease level, torque, cabling, etc.). Similarly, attention to the controller’s performance should not be overlooked.
Frequently used maintenance tests to check the condition of the gear reducers include:
Grease Analysis - A routine grease analysis checks the robot grease to monitor iron levels. Note: Intervals for PM service are based on servo hours, and it is important to reference the manual for the specific model that you have, as the hours have changed on newer robots. Also, the grease to be used should be referenced in the robot manual as well.
- Manual Test - This test entails jogging the robot to reveal worrisome indicators such as vibration and gear noise. As with other tests, this test may be helpful in determining whether a reducer is failing or has completely malfunctioned.
- Torque Analysis - Typically performed by Yaskawa Support Services or your specific robot brand manufacturer, this test measures the torque of the motors, looking for indicators that might show inconsistencies in the robot motion. Often, a spike in the data generated during this procedure will reveal any inconsistencies.
- Backlash Test - This procedure uses a dial indicator to determine the amount of backlash in the gear reducer. For accurate readings the robot and dial indicator are placed in a specific location. This is also typically administered by Yaskawa Support Services or your specific robot brand manufacturer.
While all of these checks are not always necessary, they should be utilized as needed to determine how the robot is functioning. By implementing maintenance at regular intervals and completing tasks like these, the robot’s performance is optimized, preventing unnecessary downtime.
What is the Recommended Interval for Industrial Robot Maintenance?
Robot maintenance is usually suggested every 6,000 servo-hours which is tracked in the robot. This brings up the concept of condition-based maintenance. Keep in mind that every scenario is unique, and some robots may need to be serviced more frequently (based on condition / data collected), while others may not.
With the growing demand for mass product customization with more accuracy in supply chain synchronization and faster multichannel retail responsiveness, keeping to a detailed maintenance program to maintain peak robot functionality is key to increasing uptime and staying competitive. To better facilitate this, manufacturers are realizing the importance of a
factory automation monitoring system that can monitor, accumulate and visually deliver data in real time for networked production environments. This enables data-driven optimized planning for preventative and predictive maintenance, enabling proactive decisions and, ultimately, more productive factories.
How Important is Aftermarket Assistance for an Industrial Robot?
Whether you purchase one robot or hundreds, having access to a diverse support services group can be extremely helpful to life cycle management and maximizing ROI. If you’re still thinking about making a robot purchase, it is important to buy from a supplier that offers:
- 24/7 technical support to diagnose problems remotely

- Regionally located field service technicians for rapid on-site support
- 24/7 emergency parts availability with a high First Pass Fill Rate
- IACET-accredited training at a hands-on location
- Modernization options (rebuilds, upgrades and retrofits) to increase productivity and profitability
- Robot Life Cycle Management Program customized for preventative and predictive maintenance
Robots and critical equipment can fail at inopportune times, causing downtime and unexpected costs. Taking proper precautions in conjunction with beneficial support offerings of this nature will go a long way to keeping you on the path to productivity.
Aaron Barnes is a Regional Technical Manager
Connect on: