When do you use 2D versus 3D?
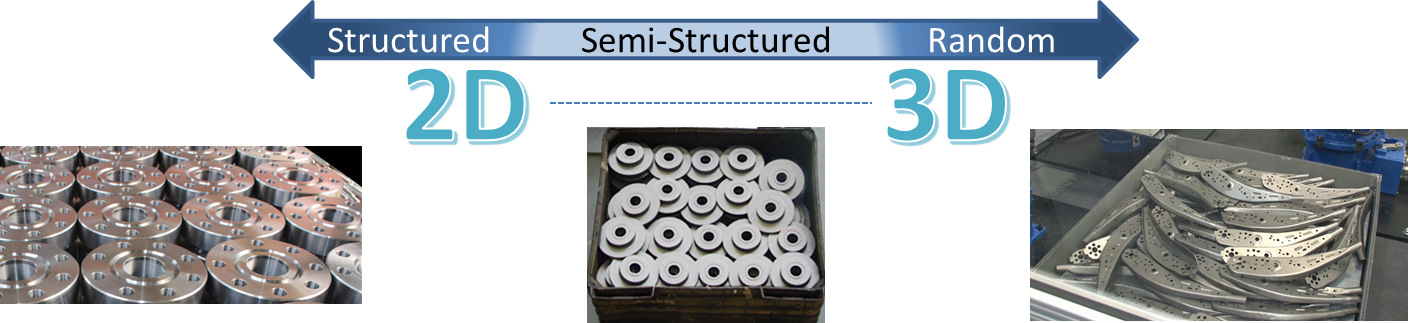
It’s all about the location and organization of the objects. If everything is very structured, and objects are positioned in a stacked or organized pattern, then 2D is the easy answer. When objects are totally randomized in position and orientation (dumped in a bin), even overlapping, then 3D is required to locate and determine the orientation. If the problem is somewhere in between, with some level of organization, either solution might work depending on the application.
The right answer is always, it depends on the application. Contact a sales representative to help find the right vision solution for you.
Powerful Vision Solutions from Yaskawa
Experience fast and reliable Vision Guided Robotics (VGR) with Yaskawa’s 2D and 3D integrated vision systems. Using industrial-grade Cognex In-Sight® cameras, most applications can be solved with MotoSight™ 2D. More complex applications, such as bin picking, which require information in all three dimensions to accurately locate objects, may benefit from Yaskawa’s MotoSight 3D BinPick solution. Other high-speed and easy-to-use robotic vision options are also available through our trusted technology partners.
MotoSight 2D
Featuring ultra-compact Cognex In-Sight 8000 series cameras, MotoSight 2D is a powerful high-speed solution that easily adds vision capability to a range of robotic tasks. Ideally suited for general robot guidance, error proofing, part identification, part inspection and high-speed picking, this easy-to-integrate hardware/software solution provides robot calibration routines and a proven tool set to help users overcome challenging applications.
Learn More
MotoSight 3D BinPick
Utilizing a high-performance Canon camera with integrated lighting, MotoSight 3D BinPick is a robust hardware/software solution that quickly and easily recognizes objects that are randomly placed in bins. Single-step recognition reduces the need for multiple cameras, while 3D CAD matching provides simplified, accurate object registration, allowing identification of complex objects without the need to train multiple images. Robust collision checking ensures the end-of-arm tool (EOAT) does not collide with the bin or other objects.